While we’re still focused on conversations on the big transition to EV technology, what’s interesting to explore is how a battery’s life isn’t over after it’s exhausted its initial application in an electric vehicle. In fact, batteries have enormous potential for reuse in stationary energy storage, all the while creating significant value. Furthermore, by bringing down the cost of storage, they can help integrate more renewable power into the grid.
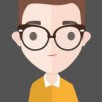
Lorem ipsum dolor sit amet, nec in adipiscing purus luctus, urna pellentesque fringilla vel, non sed arcu integer, mauris ullamcorper ante ut non torquent.
Lithium-ion batteries used in EVs, usually designed to be useful for a decade, degrade significantly during the first five years of operation. But even after 10 years of use, an EV battery can be reused in markets that need stationary energy storage requiring less frequent cycling (especially 100-300 cycles per year). The alternatives to reuse are mass disposal—possible in most regions under health and safety regulations—or recycling, which can make sense to battery makers who want to secure high-value metals, such as cobalt and nickel, and who can achieve recycling costs competitive with mining.
A second run for EV Batteries
With the continued global growth of electric vehicles (EV), a new opportunity for the power sector is emerging: stationary storage powered by used EV batteries, which could exceed 200 gigawatt-hours by 2030.
Four steps for rebirthing old EV batteries
The rapid rise of EVs could supply a storage application market with a global value exceeding $30 billion by 2030, since the second-life batteries coming out of EVs will be suitable to meet several storage applications. For a sustainable second-life battery industry to emerge, however, we must overcome several challenges that require targeted action from suppliers, end users and sector regulators.
Current battery packs vary in size, electrode chemistry, and format. These variations will only increase: By 2025, there will be up to 250 new EV models featuring batteries from more than 15 manufacturers. Each battery is designed for specific EV models, making refurbishment complex due to a lack of standardization. To overcome this challenge, automakers can design their EVs with second-life applications in mind. For example, Nissan formalized a partnership with Sumitomo Corporation to reuse battery packs from the Nissan Leaf for stationary distributed and utility-scale storage systems.
As new batteries become cheaper, the cost differential between used and new batteries will start to diminish. We estimate that, at current learning rates, the 30 to 70 percent cost advantage that second-life batteries are likely to demonstrate in the mid-2020s could drop to around 25 percent by 2040. This cost gap needs to remain sufficiently large to warrant the performance limitations of second-life batteries relative to new alternatives. To remain competitive in the face of falling new lithium-ion battery costs, firms can industrialize and scale remanufacturing processes to reduce costs and thus maintain the value gap between new and used batteries.
Stricter standards must be set for second-life battery quality, safety, and performance. A variety of global agencies and private sector coalitions—including OEMs and second-life battery companies—are getting started on creating standards that classify the performance potential of batteries across different storage applications. This will create transparency in product supply and market demand. Establishing a body to regularly review and refine battery standards and report annually on operating benchmarks and average costs could further catalyze growth in this nascent market.
There is currently no regulation outlining whether recycling or reuse is the appropriate path for an EV battery. This leads to regional differences in recycling and reuse rates, ultimately sowing uncertainties for OEMs, second-life battery companies, and potential customers about where the end-of-life product responsibility lies.
Stakeholders can proactively identify which value-maximizing path—recycling or reuse—is most appropriate, and develop new business models to fully capture the value at hand. For example, Renault engages in both recycling and reuse programs with industry partners following a structured process to determine the end-of-life pathway rooted in a regional context. This process allows it to discern whether the demand for remanufactured battery applications would make reuse preferable, or whether recycling would be the best option.
The need to dispose of millions of EV batteries in the future has already led to the emergence of recycling and reuse industries. These new industries are creating value pools that align profit with efficient resource use and enable the integration of renewable power into our grids. While many of the targeted actions listed above are already being taken on by industry players, even more forward-looking corporations and regulatory bodies can position themselves at the forefront to capture the value that second-life batteries promise.
In the Indian Scenario
While the above may seem achievable – it has to be done within the norms and standard guidelines prescribed. As far as India is concerned, the Ministry of Road, Transport, and Highways (MoRTH) has imposed strict testing and monitoring criteria for cells, battery packs, and the battery management system (BMS).
The government has recommended that these new safety regulations apply to all EVs that are allowed on public roads. The new safety requirements will also be put into effect on October 1, 2022. Heat propagation resulting from internal cell short circuits, which turns out to be a major cause of fires, are the subjects of all the additional testing and QA requirements.
More precisely, the new regulations require manufacturers to include a safety fuse for the battery that serves as a circuit breaker whenever there is an excessive amount of heat generated, a high current flow, or any other abnormal operating circumstance that produces an excessive amount of heat.
Four required sensors have also been included as a provision for monitoring and detecting these irregularities. Once tripped, the system should then notify the rider by flashing an alert on the instrument panel of the vehicle. All electric two-wheelers, as well as electric cars and cargo vehicles, will be required to adhere to these new standards established by the Automotive Industry Standards (AIS). Additionally, they state that enough cell-to-cell separation is necessary for efficient heat transmission and cell isolation.
The BMS system should incorporate technology to address over-voltage, over-charge, over-discharge, over-temperature, overcurrent, and short-circuit protection in the case of electric two-wheelers in particular. Last but not least, in order to prevent overcharging, the chargers for the vehicles must also feature a voltage and time-based cut-off.
Your Comment Please