A variety of innovative techniques to modify the active material particle structure have been implemented throughout the years. These techniques include particle coating, grain- boundary strengthening, designer secondary particles, and single crystal morphology. Particle coatings improve the structural strength of the secondary particle providing longer cycle life and improved capacity retention. Unique secondary particle structures like core–shell and full-concentration-gradient exhibit local regions of high-Ni content as well as high-Mn content combining increased capacity and structural stability.
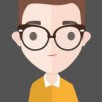
Lorem ipsum dolor sit amet, nec in adipiscing purus luctus, urna pellentesque fringilla vel, non sed arcu integer, mauris ullamcorper ante ut non torquent.
Distinctly shaped secondary particles (cube, rod, dumbbell, needle) synthesized through the common co-precipitation technique have been shown to exhibit superior performance. Secondary particles with radially aligned primary particles have been shown to improve high C-rate performance by offering faster solid-state diffusion pathways for the Lithium ions.
Radial alignment of primary particles is also beneficial in the uniform distribution of the mechanical stress caused due to volume changes during cycling. Designer secondary particles offer distinct enhancement in different aspects of battery performance metrics. Single crystal morphology eliminates the problem of micro-cracking, giving better degradation performance and long cycle life.
These particle structure modification techniques prove effective in tackling particle-scale challenges in the electrode microstructure.
Foreseeable Challenges
Low electronic conductivity Most cathode-active material particles have low electronic conductivity. Conductive additives (carbon black, acetylene black) need to be added to provide electronic percolation networks and the three-phase boundary necessary for electrochemical reaction. Uniform distribution of the conductive additives in the electrode and on the surface of active material particles is not guaranteed by the traditional slurry casting process. Synthesizing composite particles of active material and conductive additives offers one approach to tackle this challenge.
Slow solid-state diffusion For complete utilization of the available capacity, Li ions need to diffuse to the core of the secondary particle. Randomly oriented primary particles cause tortuous diffusion. This sluggish solid-state diffusion of Li ions results in underutilization of the active material at high C-rates and impacts the rate capability performance of the battery. Large secondary particles increase the energy density, but particle size is limited by solid-state diffusion. Engineering techniques producing secondary particles with radially-aligned primary particles alleviate this challenge to some extent by reducing intra-particle anisotropy and providing faster diffusion pathways.
Micro-cracking Large anisotropic expansion and contraction of the active material crystals during cycling is problematic for the particle’s structural integrity. The mechanical stress caused by such large volume changes introduces micro-cracks along primary particle boundaries. These cracks increase the electrolyte infiltration in the secondary particle causing capacity reduction due to deleterious particle-electrolyte side reactions. The cracks widen up and propagate during subsequent cycles causing fragmentation of the secondary particle and electrical isolation of localized regions. The challenge is to avoid such micro-cracking which results in reduced capacity, underutilization of active material, and short cycle life. Particle designs like core–shell, full concentration gradient, radially-aligned primary particles as well as different particle coatings have been proved effective in avoiding such micro-cracking.
Particle size optimization Size distribution of active material particles making up the electrode affects the electrochemical performance. Too large particles cause active material underutilization at high C-rates due to longer solid-state diffusion paths. While too small particles increase the active surface area available for the deleterious side reactions causing faster chemical degradation. A sensible PSD through the electrode microstructure can optimize the electrochemical performance. Particle engineering and design techniques offering control over the particle size prove effective in generating such optimized particle size distributions.
Consistency and scalability Ensuring consistency of a novel particle engineering technique during scale-up poses a challenge before successful commercialization. Although, advantages of the core–shell and concentration gradient particle structures have been known since 2005, commercialization of this synthesis technique has been slow. Issues like complex co-precipitation procedure, transition metal segregation during calcination are at the core of this slow commercialization. Similarly, complex synthesis procedures generating single crystal morphology suffer from cost and scalability issues for large scale production. Large number of production variables influence the product properties therefore it is important to understand the process–product relationship.
Such understanding can be developed through systematic experimentation and process modelling studies. Systematic investigation of scale-up issues are required to ensure lab-scale observations of improved electrode performance due to particle design hold true at industrial scale. Advances in science and technology to meet challenges Variety of particle structure modification and particle coating techniques are being investigated by researchers. The core–shell and concentration gradient secondary particle structures show promise in simultaneously achieving high capacity offered by high-Ni content at the core and high structural stability offered by high-Mn content at the particle surface.
Post-processing of as received NMC11 particles to generate porous nano-structured secondary particles has proved beneficial. This structure is achieved by ball-milling and further spray drying of active material powder. The primary particle size and porosity of the nano-structured secondary particle can be adjusted by controlling the calcination temperature. The nano-structured secondary particles exhibited strong structural integrity and enhanced capacity retention.
Particle coating improves cycle life by increasing structural strength and reducing particle-electrolyte side reactions. Whereas, grain-boundary strengthening technique further reduce the electrolyte penetration inside the secondary particle. Advances are being made to ensure uniformity of such coatings on the active material particle surface. Coating conductive additives on the secondary particle surface is also being investigated for more homogeneous distribution of conductive additives through the electrode microstructure. Advances are being made to discover dopants that favorably alter the secondary particle morphology. Small amounts (∼1%) of dopants are added during the synthesis procedure of the active material. After calcination, altered secondary particle structure is observed. Doping high-Ni NMC particles with small amounts of multivalent ions like Zr, Al, Ti, Mg, T, B, Nb, Mo, Ta, W has improved structural stability and electrochemical properties [16–18]. Some dopants cause radial-alignment of the primary particles. As discussed before such radially-aligned primary particles provide faster diffusion pathways for Li ions as well as reduce the severity of micro-cracking by uniformly distributing the mechanical stress caused by volume changes during cycling. Synthesis of single crystal AM particles is getting traction for high-Ni chemistries. Single crystal morphology eliminates the phenomenon of micro-cracking increasing the battery cycle life. Many of these particle engineering techniques can be implemented together to achieve optimum particle-scale performance.
Combining different particle-scale engineering techniques offers a promising approach to extracting additional energy and power densities from the Li-ion batteries. Well-developed techniques can be further used for the manufacturing of thick electrodes and recycling of the active materials. Systematic studies are required to fully realize the potential of various particle engineering techniques.
Your Comment Please