Lithium-ion batteries are the beating heart of our modern technological world, powering everything from smartphones and laptops to electric vehicles and renewable energy storage solutions. These compact energy storage devices have revolutionized our daily lives, enabling portable electronics to function seamlessly and electric vehicles to hit the road with reduced carbon emissions. To fully appreciate the capabilities of lithium-ion batteries, it’s crucial to understand the intricate journey they undergo, from sourcing raw materials to assembly, testing, and quality control. In this article, we’ll take a deep dive into the fascinating world of lithium-ion battery manufacturing.
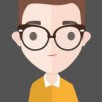
Lorem ipsum dolor sit amet, nec in adipiscing purus luctus, urna pellentesque fringilla vel, non sed arcu integer, mauris ullamcorper ante ut non torquent.
Raw Material Sourcing
The journey of a lithium-ion battery begins with the sourcing of raw materials, some of which are elemental, while others are compounds critical to its construction. These materials include:
1) Lithium: The star of the show, lithium is the lightest metal on the periodic table and the main component of a lithium-ion battery’s anode. The majority of lithium reserves are found in countries like Australia, Chile, and China.
2)Cobalt: Cobalt is a crucial component of the cathode in many lithium-ion batteries, providing stability and increasing energy density. A significant portion of the world’s cobalt supply comes from the Democratic Republic of Congo.
3) Nickel: Often combined with other materials like cobalt and manganese, nickel helps improve the energy density of lithium-ion batteries. Nickel mining is widespread globally.
4) Graphite: Graphite serves as the anode material in lithium-ion batteries. It is typically sourced from countries like China, Brazil, and Canada.
5) Aluminum and Copper: These metals are essential for constructing the battery’s casing and conducting electricity within the cell. They are readily available through mining and recycling processes.
Material Refinement and Processing
Once raw materials are sourced, they undergo refinement and processing to meet the stringent specifications required for battery manufacturing. This includes:
1) Purification: Raw materials like lithium and cobalt are purified to remove impurities that could hinder battery performance.
2) Chemical Compounding: Elements like nickel, cobalt, and manganese are blended in specific ratios to create cathode materials with the desired properties.
3)Coating: Electrode materials, such as graphite for the anode and the cathode materials, are coated onto thin foils made of copper and aluminum, respectively. These coated foils will become the heart of the battery’s energy storage.
Battery Cell Assembly
The assembly of a lithium-ion battery cell is a complex and precise process, involving several key steps:
1) Electrode Winding: The anode and cathode foils, coated with their respective materials, are wound into a jelly-roll-like structure, ensuring that the materials remain separated but in close proximity.
2) Electrolyte Filling: The jelly-roll structure is immersed in a liquid electrolyte solution, typically a lithium salt dissolved in a solvent. The electrolyte facilitates the flow of lithium ions between the anode and cathode during charging and discharging.
3) Sealing: The battery cell is sealed to prevent the escape of electrolyte and maintain a controlled environment inside. This seal ensures the safety and longevity of the battery.
4) Formation: The newly assembled battery cell undergoes a “formation” process, where it is charged and discharged multiple times to activate its electrochemical properties and stabilize its performance.
Battery Module and Pack Assembly
Individual battery cells are combined into modules, and these modules are then assembled into battery packs, depending on the application. This process is tailored to meet the specific requirements of electric vehicles, portable electronics, and other devices. It involves:
1) Thermal Management: Battery modules and packs often include thermal management systems to regulate temperature during operation, preventing overheating and maintaining optimal performance.
2) Voltage and Current Balancing: Balancing circuits ensure that each cell in a module or pack is charged and discharged evenly, extending the lifespan of the battery.
3) Housing and Encapsulation: Battery modules and packs are enclosed in protective casings to safeguard against physical damage and to insulate against moisture and contaminants.
Testing and Quality Control
Rigorous testing and quality control are essential in ensuring the reliability and safety of lithium-ion batteries. This stage includes various assessments, such as:
1) Capacity Testing: Battery cells, modules, and packs undergo capacity testing to determine their ability to store and deliver energy effectively.
2) Cycle Life Testing: Lithium-ion batteries are subjected to numerous charge and discharge cycles to evaluate their long-term durability.
3) Safety Testing: Batteries are subjected to a range of safety tests, including puncture and crush tests, to assess their resistance to physical damage.
4) Thermal Testing: Batteries are exposed to extreme temperature conditions to evaluate their performance and safety in different environments.
5) Environmental Testing: Battery packs are tested for resistance to moisture, dust, and other environmental factors that may affect their performance.
Recycling and End-of-Life Management
Lithium-ion batteries have a finite lifespan, after which they may no longer meet the performance requirements of their initial application. Proper recycling and disposal are crucial to mitigate environmental impact and recover valuable materials. Recycling processes involve:
1) Collection: Old or spent batteries are collected from various sources, including electronic waste recycling centers and automotive service centers.
2) Disassembly: Battery packs are disassembled into individual cells, modules, and components.
3) Material Recovery: Battery materials, such as lithium, cobalt, nickel, and graphite, are recovered through various recycling techniques.
4) Environmental Management: Proper disposal and recycling of battery components are essential to prevent environmental contamination and reduce waste.
The Crucial Role of Standards and Protocols in Lithium-Ion Battery Manufacturing
Lithium-ion batteries have become ubiquitous in our modern world, powering everything from mobile devices to electric vehicles and renewable energy storage systems. As these batteries continue to advance in technology and proliferate across various industries, the importance of standards and protocols in lithium-ion battery manufacturing cannot be overstated. They serve as the cornerstone for ensuring safety, performance, and interoperability in the production of these essential energy storage devices.
- Safety Assurance
Safety is paramount in lithium-ion battery manufacturing, as these devices store and release electrical energy. Standards and protocols are essential for mitigating the risks associated with battery manufacturing, including thermal runaway, leakage, and even fires.
a) Testing Standards: Manufacturers adhere to specific testing standards to evaluate a battery’s safety characteristics. These standards include testing for thermal stability, overcharge protection, and puncture resistance. Compliance with these standards helps ensure that batteries are resistant to abuse and can safely withstand various conditions.
b) Manufacturing Guidelines: Standards provide guidelines for the design, construction, and assembly of batteries to minimize the potential for manufacturing defects that could lead to safety hazards. They define acceptable practices to prevent issues like internal shorts, overheating, and electrolyte leakage.
c) Regulatory Compliance: Many countries have regulations that mandate adherence to established safety standards for lithium-ion batteries. Compliance with these regulations is essential for product certification and market access.
- Performance Consistency
Uniformity and consistency in battery performance are vital to meet the expectations of end-users and ensure the reliability of devices and systems powered by lithium-ion batteries.
a) Capacity and Cycle Life: Standards and protocols specify performance parameters, such as capacity (measured in ampere-hours or watt-hours) and cycle life (the number of charge and discharge cycles a battery can endure). These parameters help manufacturers produce batteries that consistently meet defined performance expectations.
b) Charge and Discharge Rates: Standards also dictate acceptable charge and discharge rates, ensuring that lithium-ion batteries can be charged and used safely within specified limits without compromising their performance or lifespan.
- Interoperability
In today’s interconnected world, where lithium-ion batteries are integrated into a wide range of devices and systems, interoperability is essential. Standards and protocols play a pivotal role in ensuring that batteries from different manufacturers can seamlessly work together.
a) Connector Standards: Standards for battery connectors, such as those for electric vehicles, portable electronic devices, and renewable energy systems, help ensure that batteries can be easily integrated into various applications without compatibility issues.
b) Charging Protocols: Standardized charging protocols and connectors, like the USB Power Delivery (USB-PD) or CCS (Combined Charging System) for EVs, simplify the charging process and allow different devices and vehicles to share common charging infrastructure.
c) Communication Protocols: In some applications, batteries communicate with other system components for optimal performance. Standardized communication protocols ensure that batteries can exchange information effectively with other devices and systems, enhancing overall functionality.
- Quality Control
Standards and protocols provide a framework for quality control throughout the manufacturing process, from raw material sourcing to assembly and testing.
a) Material Quality: Manufacturers adhere to standards that specify acceptable levels of impurities and contaminants in raw materials like lithium, cobalt, and nickel, ensuring that the battery’s performance and safety are not compromised.
b) Manufacturing Processes: Standards guide the manufacturing processes, from electrode coating to cell assembly, to ensure that each step meets defined quality criteria.
c) Quality Testing: Protocols detail the testing procedures that batteries must undergo to verify their safety and performance characteristics. These tests help identify and rectify any manufacturing defects before the batteries reach the market.
- Environmental Sustainability
As environmental concerns become increasingly important, standards and protocols also address the sustainable manufacturing and disposal of lithium-ion batteries.
a) Recycling Guidelines: Standards outline guidelines for recycling lithium-ion batteries, encouraging manufacturers to implement environmentally responsible end-of-life management practices. These guidelines promote the recovery and reuse of valuable materials, reducing waste and environmental impact.
b) Compliance with Regulations: Compliance with international environmental regulations, such as the European Union’s Battery Directive, is facilitated by adherence to specific standards and protocols related to the materials used and recycling practices.
The journey from raw material sourcing to the assembly of lithium-ion batteries is a highly intricate and well-orchestrated process. These batteries, which power the devices and vehicles that have become indispensable in our daily lives, rely on a complex supply chain and a careful balance of materials, precision engineering, and quality control.
As technology advances, we can expect continuous improvements in lithium-ion battery manufacturing processes, resulting in higher energy densities, longer lifespans, and even safer batteries. Additionally, sustainable practices, such as recycling and responsible raw material sourcing, will play an increasingly critical role in ensuring the environmental and ethical sustainability of lithium-ion battery production. With these developments, lithium-ion batteries are poised to continue transforming the way we live, work, and travel for years to come.
Your Comment Please